Insights from Aptiv: Exploring the future and sustainability in Manufacturing
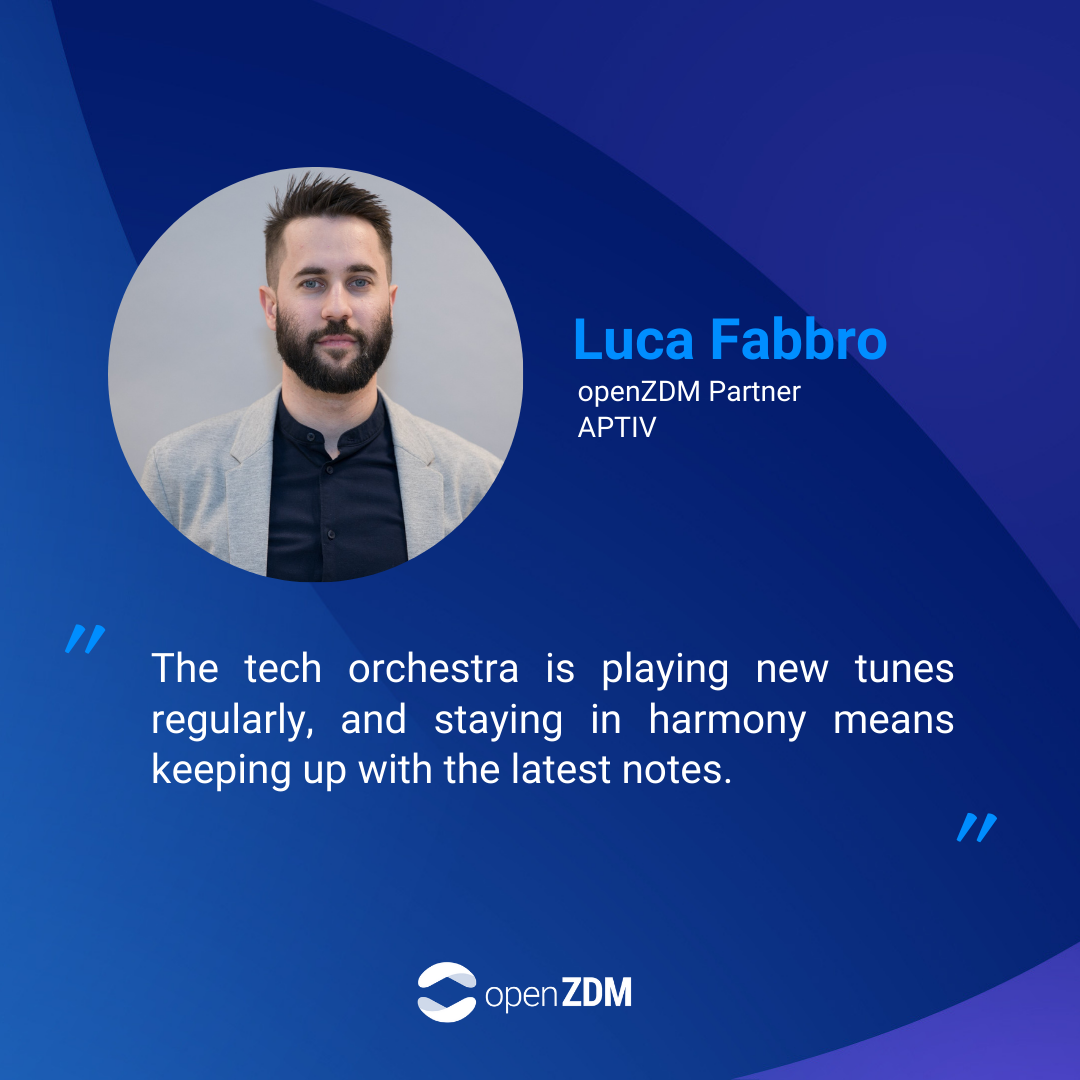
It was our greatest pleasure to interview Luca Fabbro, openZDM partner and IT Technical Operations Analyst in Aptiv on the Future of Manufacturing & Sustainability. Here is what we found out.
1. How do you foresee the role of digitalisation shaping the future of manufacturing processes?
Digitalization is the new approach that is overwhelming today’s manufacturing. With technologies like IoT, AI, and advanced data analytics, we’re looking at a future where machines communicate seamlessly, processes are optimized in real time, and predictive maintenance becomes the norm. This isn’t just about efficiency; it’s a complete overhaul of how things are made.
2. What are the challenges and opportunities you see in achieving sustainable manufacturing practices, and how can manufacturers balance sustainability with economic considerations?
Balancing sustainability and economic considerations is like walking a tightrope, but it’s a necessary act for the future. One challenge is the initial cost of implementing sustainable practices.
It’s like investing in a good pair of shoes—it might be pricey at first, but it pays off in the long run.
Manufacturers need to see sustainability as an investment rather than a burden. Green technologies are advancing rapidly, and those who embrace them early gain a competitive edge. Plus, consumers are becoming increasingly eco-conscious, so there’s a market waiting for products with a green stamp.
To strike the balance, it’s crucial for manufacturers to adopt a holistic view. Consider the entire life cycle of a product, from raw material extraction to disposal. Sustainable practices aren’t just about appeasing environmentalists; they can lead to cost savings, efficiency improvements, and a positive brand image.
3. How can manufacturing engineers leverage data analytics and artificial intelligence to optimize production processes and improve product quality?
By collecting and analyzing data from various points in the production process, engineers can uncover patterns and insights that were once hidden in the manufacturing fog.
AI can predict when a machine is about to throw a tantrum and suggest preventive maintenance. It’s like having a clairvoyant mechanic.
Quality control becomes a easier with AI-powered image recognition and defect detection. Optimizing production becomes easier with AI algorithms fine-tuning processes in real time. It’s not just about speed; it’s about efficiency and reducing waste.
4. What role do the manufacturers play in facilitating the transition from Industry 4.0 to Industry 5.0, and what skills are crucial in this context?
Manufacturers are the conductors of this path. In the transition, they become orchestrators of a more human-centric approach. While Industry 4.0 introduced automation and data exchange, Industry 5.0 puts humans at the forefront, working hand-in-circuit with machines.
Crucial skills for manufacturers in this transition include adaptability, as they navigate the evolving landscape. Collaboration is key, as Industry 5.0 blurs the lines between man and machine.
Manufacturers must also embrace continuous learning. The tech orchestra is playing new tunes regularly, and staying in harmony means keeping up with the latest notes. It’s a shift from just mastering the machines to mastering the symphony they create with humans.
Short Biography
Luca Fabbro works as IT Technical Operations Analyst in Aptiv, taking care of special projects and continuous improvements in the manufacturing process.
During his professional experience in Aptiv, Luca developed different projects within the company such as:
– AI model for preventive maintenance of molding tools;
– Real time quality data collection, by removing the usage of paper, increasing the efficiency and tracking of products’ lifecycle.