Insights from VDL Weweler: Exploring the future and sustainability in Manufacturing
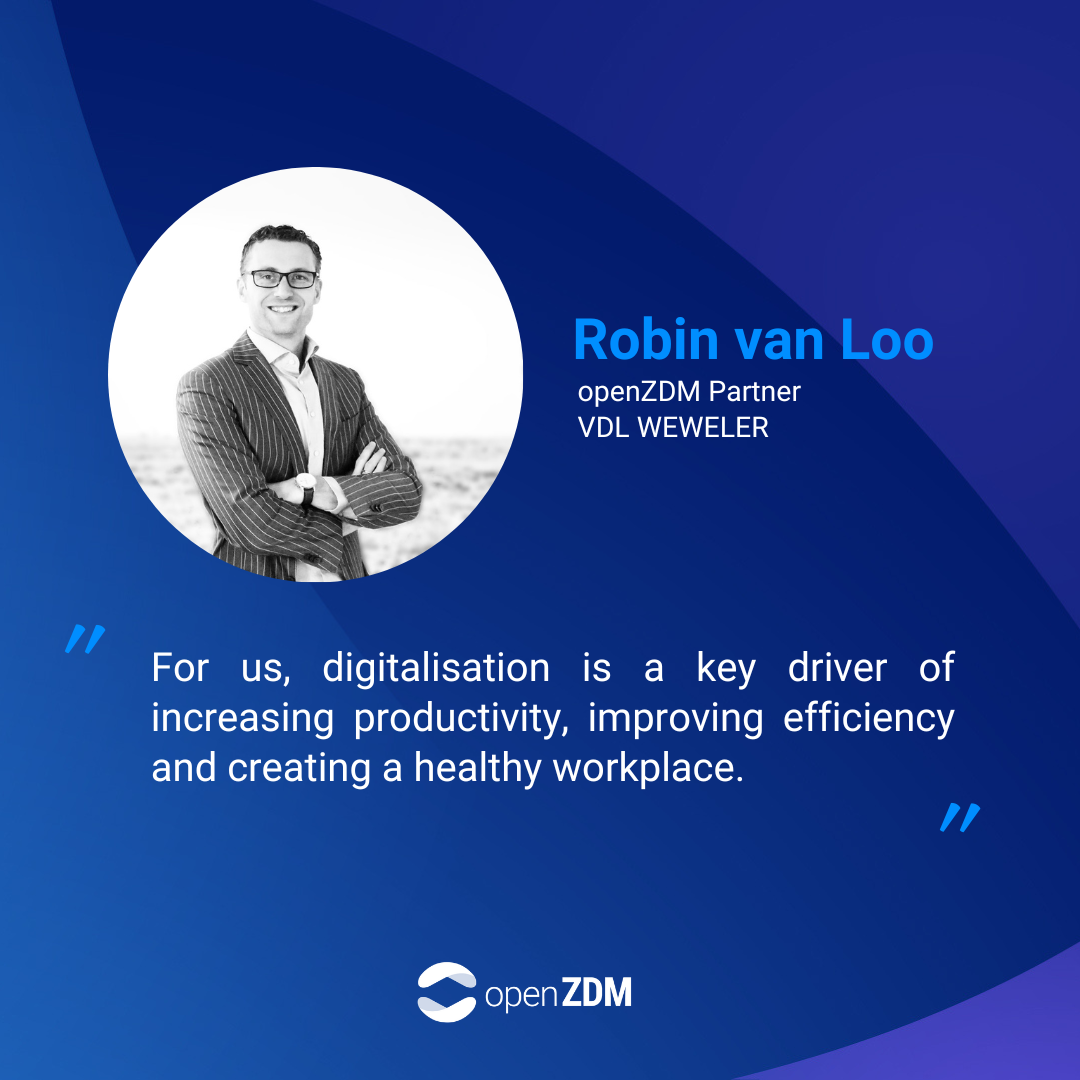
We had an exciting discussion on the Future of Manufacturing & Sustainability with Robin van Loo, Manager Operations at VDL Weweler – one of the openZDM’s partners. In this article, we are discovering all tips we found out.
1. How do you foresee the role of digitalisation shaping the future of manufacturing processes?
Digitalisation has been at the heart of the design of the factory of VDL Weweler when it was built in 2012. For us it is a key driver of increasing productivity, improving efficiency and creating a healthy workplace.
Automation and robotization reduces the physical workload for operators, but also implies a change from manual craftsmanship to data driven process control. In a tight labour market it is important to maximize factory output without increasing the work force.
At the same time digitalisation is a great aid in improving product quality and quality control, reduction of waste and optimisation of energy consumption. These factors are key in the realisation of our sustainability goals.
2. As an expert, what initiatives do you think can be implemented to reduce the environmental impact of manufacturing operations and promote sustainability?
Global warming and climate change require immediate action from everybody to adapt and change to a more sustainable mode of operations. Digitalization provides vast amounts of data, but data in itself will not bring forth the next step in the reduction of environmental impact.
As prof.dr. Dipak C. Jain said: “Knowledge comes from analysis, wisdom comes from synthesis”.
Companies must invest in understanding data and bring all insights together to make the next step. This does not require major projects or investments, but far more an attitude of just start doing it. Challenge the status quo,
reduce the amount of waste and seek less energy intensive alternatives.
3. What potential challenges do you foresee in the widespread adoption of Industry 4.0 technologies, and how can they be mitigated?
The adoption of Industry 4.0 gives a paradigm shift from manual labour and craftsmanship to digital process control. Whilst this improves productivity greatly without the need for more labour, it also requires more high skilled staff in the process and automation engineering roles.
Smart technologies, connectivity and digitalization provide us with vast amounts of data, but translating data into real-time, operational insights is not as straight forward as it may seem.
At the same time the dependency on and complexity of technology and data communication increases almost exponentially, making the production system more susceptible to interferences and breakdowns. This challenges us to also implement mitigation strategies to continue production safely in such events.
I always compare this to flying an airplane: normal operations are done using the optimal conditions provided by the auto-pilot, but if something goes wrong you must always have the option to safely land manually.
4. In your opinion, what industries or sectors are most likely to benefit from the advancements brought about by Industry 5.0, and how can manufacturers prepare for
this transformation?
Industry 5.0 adds onto Industry 4.0 by focusing on sustainability, human interaction with the available digital tools and putting people central again at the heart of the company. I think any industry or sector can benefit from the advancements, but is depends at the current state of a company whether they have the maturity yet to make the next step.
Over time it will not be the question whether you will implement Industry 5.0, but only when you will be ready for it. Manufacturers must prepare for this change and seek cooperation and partnerships in making the transition.
Industry, research companies and universities should join forces and collaborate in the development of Industry 5.0, not only to improve next quarter’s results, but also to speed up long term goals with respect to
sustainability and human well-being.
Short Biography
Robin van Loo is the Manager Operations at VDL Weweler, responsible for daily operations and technical support of the manufacturing department. Over the last nearly 100 years VDL Weweler has developed into a leading international designer and manufacturer of (air) suspension solutions for trailers, trucks and busses.
With an educational background in both engineering and business administration Robin promotes the participation in projects like openZDM to continuously improve operations and share knowledge with partners.