What is an NDI system for zero defects?
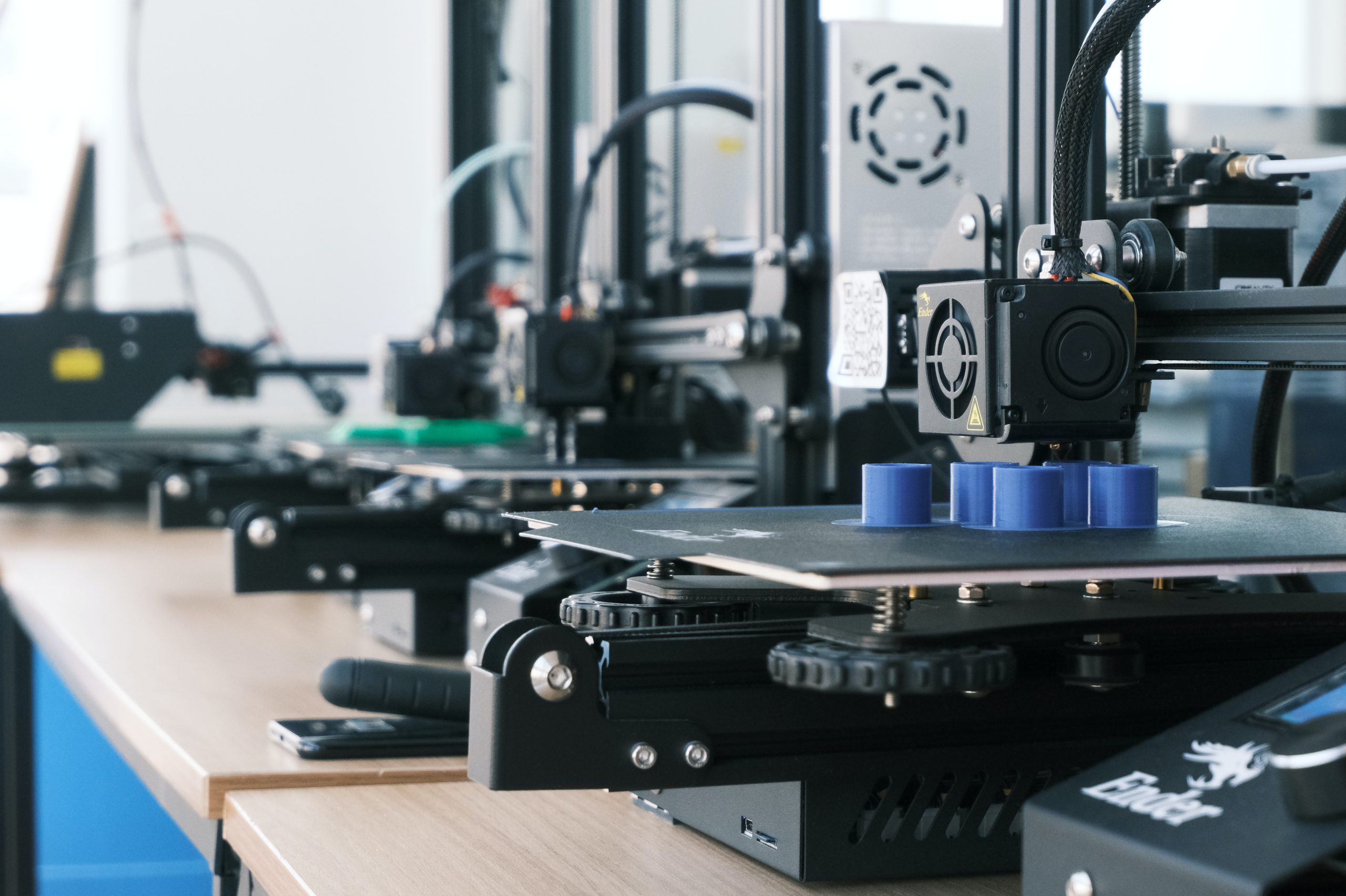
Valentina Pasquinelli and Vittoria Medici, two accomplished PhD students from the Polytechnic University of Marche, are happy to be featured in the fifth installment of the exclusive insights and professional perspectives from the openZDM project partners.
One of the core elements of the openZDM project is the deployment of NDIs which is an acronym for Non-Destructive Inspection systems.
What are NDIs?
NDIs are a Zero-Defect Manufacturing tool used to inspect and measure different features of the production processes according to the different pilot use cases in the openZDM project.
NDIs are fundamental to tend towards the ZDM paradigm controlling the quality of the product at different stages of the production process, in order to prevent defects from propagating along the line.
The main way to ensure 100% defect-free products is to inspect every quality characteristic, in all items and from the earliest stages of the production process. Therefore, ZDM is crucially important to reduce waste and increment the sustainability of the whole production process.
Non-destructive inspection methods exploit data-driven quality assessment techniques for online defect identification and quality assessment. The NDIs developed are based on different innovative technologies such as: vision system in the Visible (VIS) and Infrared (IR) range, laser line triangulation
systems, X-ray diffraction analysis.
These quality control stations are installed in-line in the various pilot use cases of the openZDM project, but they are more complex than a non-destructive testing in the common meaning. NDIs are an edge computing system, that can improve value of big data. A series of NDIs can generate a distributed edge computing system. The combination of different technologies in different stages of the manufacturing process can increase the potential of using non-contact testing, making NDIs place where knowledge starts to take form.
The NDIs are the first links between analogue reality and cyberspace, comprising physical objects and digital ones, as Cyber-Physical Systems (CPS), the key nodes of the Smart Factory.
Architecture of an NDI
Their architecture can vary a lot according to the used technology and the environment in which they operate. However, a common architecture can be identified.
Each Non-Destructive Inspection system is composed of a hardware part and a software part, who work combined to extract and analyze the features of interest.
The hardware part is a digital acquisition system which includes:
• the sensors or measurement system, in charge of obtaining raw data
• actuators in charge of executing the test sequence
• the electronics for the acquisition of sensors data
• the processing unit that turns data into value-added information and/or knowledge
The software part should allow:
• the management of the sensor and the digital acquisition system
• the processing to extract characteristic features from the raw data
• the conformity assessment
Summary
NDI (Non-Destructive Inspection) systems are a powerful tool to inspect 100% of product, in different stages of the process, providing a complete picture of product quality. Detect features about the process and the manufactured product, is one of the main strategies of Zero-Defect Manufacturing. It
enables repair actions or a preventive approach thanks to new technologies such as Digital Twin services and Data Analytics tools.
Hardware and software together, integrated with the complex cyber-physical industrial facility, can share valuable information about the product and different KPIs that can help to optimize the manufacturing process. NDIs contribute therefore to the digitalization of the factory providing the
means to detect and prevent defects in different use case scenarios.
To discover more about the installation of NDIs in the openZDM project watch the interview to Milena Martarelli, Associate professor at the Polytechnic University of Marche from Italy who talks about the meaning of NDIs in the openZDM project: