openZDM is assessing 4 innovative technologies that will elevate the Manufacturing industry
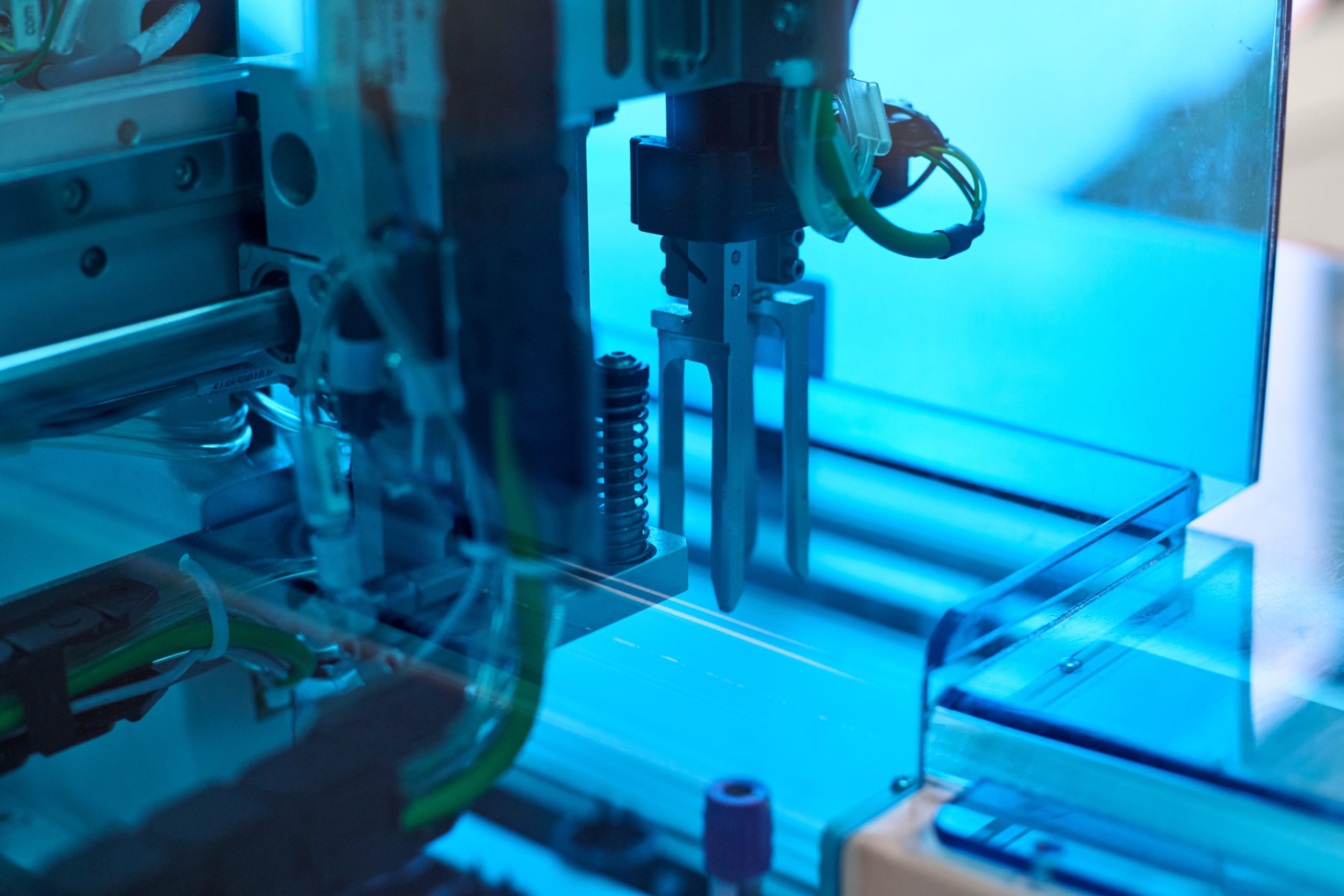
In the fourth instalment of the exclusive insights and expert opinions from the openZDM project partners, we are delighted to showcase the work of talented PhD students from Polytechnic University of Marche, Valentina Pasquinelli and Vittoria Medici.
The openZDM project aims to provide an open platform through the installation of a series of Non-Destructive Inspection (NDI) systems based on 4 innovative technologies: Visible (VIS) range, Infrared (IR) range, Laser line triangulation systems and X-ray diffraction.
Visible (VIS) range
openZDM exploits inspection systems in the visible range to deeply analyse the product and extract valuable information that can be used for process control and diagnosis. The use of cameras in the visible range opens infinite possibilities towards the postprocess of the data (fault detection, clustering, pattern recognition, geometric matching etc.) and can be adapted to any use case, from harsh environments to stationary applications.
Vision based techniques are used in the VDLWEW (steel industry) and APTIV (battery production) use cases to inspect aesthetic defects that could have an impact on the mechanical resistance of the product. In the VIDRALA use case (bottle industry), a high-speed camera grabs images related to specific features of the glass bottle production process.
Source: https://www.mapvision.fi/blog/multi-camera-technology, https://www.rnaautomation.com/products/bespoke-automation/vision-inspection-systems/
Infrared (IR) range
IR Thermography is the technology that best suits to obtain the thermal distribution of a product in a non-intrusive way. Every existing object emits radiation in the infrared spectrum, which is an indicator of the object’s temperature. The thermal camera sensor converts the infrared radiation coming from the measurand into a digital matrix of temperature values.
It allows measurements:
- fast;
- at very high temperature;
- on motion objects;
- of thermal gradients.
Source: Optris catalogue
IR Thermography is used in two different stages of the VDLWEW Ecoline to evaluate if non-uniformity in the distribution of the bar could affect the overall performance of the next stages of the production process, generating defective products. In the bottle industry VIDRALA use case, thermal images are a powerful tool to estimate the bottle wall thickness. In the APTIV use case, thermography is used for texture analysis, allowing to perform inspections of the welded joints that connect the battery cells.
Laser line triangulation systems
Laser line triangulation systems allow shape detection without contact and are extremely flexible, therefore can open infinite possibilities of application.
In the VDL WEWLWER use case, the laser line triangulation technique is used to inspect the trailing arm at different stages of the production process:
- Before and after thermal treatments, to measure the straightness of the raw product. At high temperatures, environmental conditions are very harsh making the development of this system a real challenge.
- At the end of the production process, to carry out a 3D robotic inspection of the complete geometry of the trailing arm.
Source: https://www.automationtechnology.de/cms/wp-content/uploads/2021/07/C5-Series_web.pdf
In the VWAE use case, the triangulation system, developed by U-Sense, is a portable and wireless device which allows gap and flush measurement of the car in the Body Shop and in the Final Assembly Line.
X-ray diffraction
X-ray diffraction is a non-destructive technique which can be used to measure the surface tension of the component. Thanks to this innovative technique it is possible to determine if the inspected component contains residual stresses which could be responsible for future deformations of the product when it undergoes thermal or mechanical treatments. The measurement of residual stresses using X-ray diffraction enables engineers to assess the structural integrity of the components and predict their performance under different loading conditions.
Source: https://unixray.com/top-10-industrial-x-ray-machine/
In the VDL WEWELER use case, X-ray inspection allows to measure surface tension of the raw product and correlate this stress to the non-straightness of the trailing arm. The same measurement is carried out at the end of the process in significative points of the product.
Conclusions
Thanks to the 4 non-destructive technologies presented, the openZDM project shows great potential in detecting defects or anomalies in the manufacturing processes.
These innovative technologies (visible and infrared range vision, laser line triangulation and x-ray diffraction systems) can be used individually or combined to have an in-depth understanding of the product features, providing value-added information that can be shared through the openZDM platform.
As Zero-Defect Manufacturing requires, non-destructive technologies installed inline, inspecting 100% of the products, provide a complete picture of the process, driving the manufacturing industry towards an innovative approach in quality control.