Interview: openZDM through the eyes of the Project Coordinator
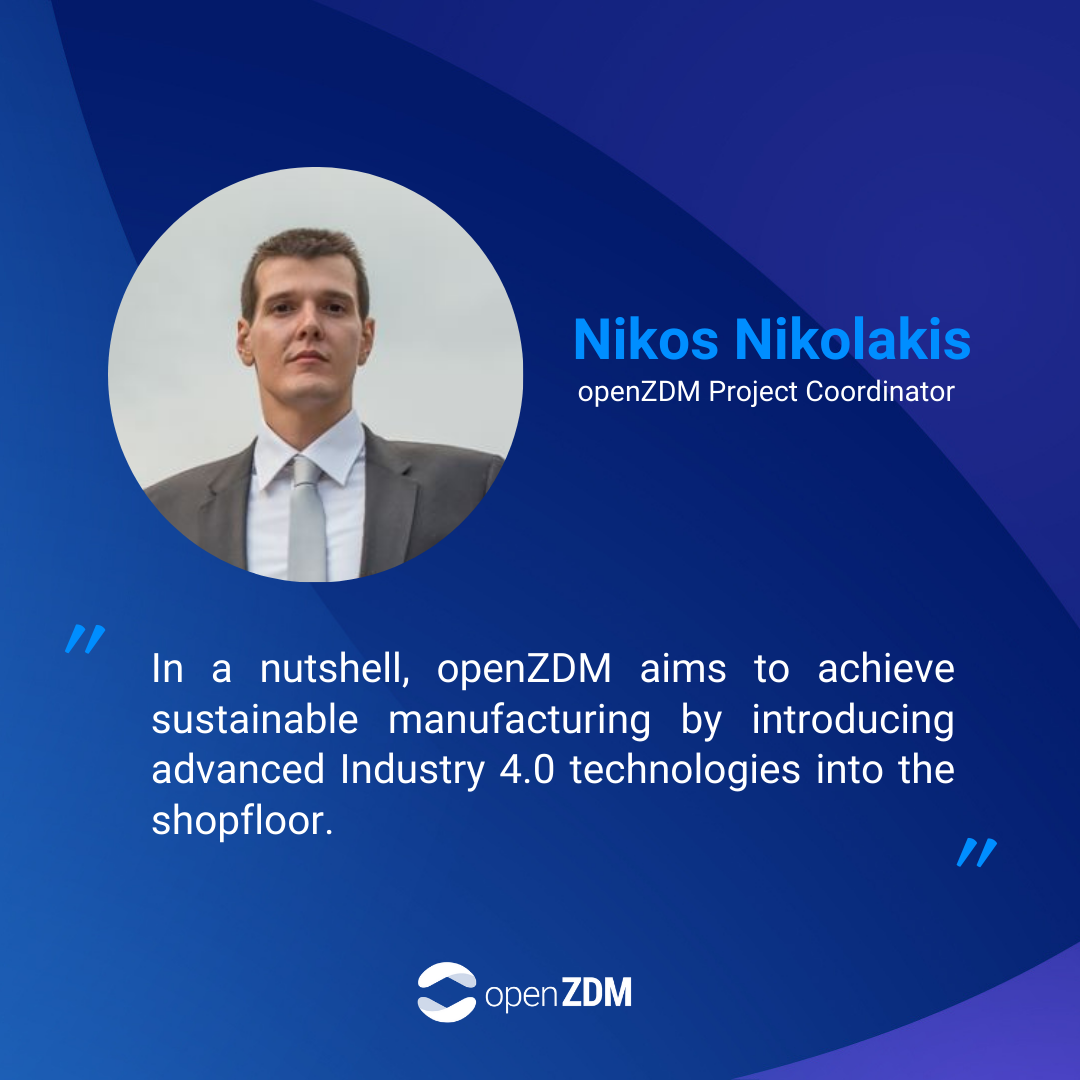
It was our greatest pleasure to interview Dr Nikos Nikolakis, openZDM project coordinator and to learn more on his standpoint about manufacturing trends and the role of openZDM project in this innovative industry. Here is what we found out.
What sustainable manufacturing practices and technologies are being developed and promoted through the openZDM project?
openZDM aims to provide intelligent edge solutions allowing manufacturers to efficiently use their data towards proactively identifying quality defects and manage them effectively, thus, reducing waste.
In a nutshell, openZDM aims to achieve sustainable manufacturing by introducing advanced Industry4.0 technologies into the shopfloor, including but not limited to the following:
- The deployment of non-destructive inspection tools on the shop floor allows for proactive control strategies to be implemented making manufacturing processes cost-effective while helping to achieve environmental goals, such as energy and material reduction.
- The introduction of AI and ML in tandem with digital twins and LCA for online quality assessment and manufacturing process optimization, evaluating production goals but also environmental ones, through an LCA at a process level.
In what ways does the openZDM project foster collaboration and knowledge exchange among European manufacturers for sustainable manufacturing?
The openZDM project supports knowledge acquisition and exchange, based on collaboration, peer-to-peer learning, experimentation, and risk-taking.
The project will offer opportunities for investigating NDI solutions for manufacturing, digital twin, AI and AAS, and their deployment in industrial environments. This will be achieved by working in tandem with European associations and working groups on how to promote further research based on the results of the project.
This is also expected to significantly contribute to the enrichment of academic curricula as well as the knowledge capabilities of academic and research organisations. In turn, this will allow for extensive follow-up research at the participating companies in order to transfer the generated knowledge and experience to third parties (i.e. industrial partners, other research centres, etc) distributing acquired knowledge across Europe.
How is the openZDM project addressing the challenges and opportunities brought about by Industry 4.0 in the manufacturing sector?
The manufacturing sector is reportedly amid its transformation to Industry4.0. The digitally enabled factory provides a great number of potential solutions and technologies to improve several aspects of it. However, many companies still rely on older methods. In practice, there are several challenges for companies across the EU for implementing Industry4.0, such as lack of awareness and education, lack of funds, resistance to change and macroeconomic strategy, lack of infrastructure, and so on and so forth.
Despite the challenges there are significant opportunities stemming from implementing industry4.0.
In this context, openZDM brings together stakeholders from the industry, academia, and technology providers, to work together towards raising awareness, develop incentives, contribute to the development of policies and regulations aligned with industry4.0, by developing and demonstrating its solution for continuous quality assessment and control towards a ZDM. The novelty of the proposed system is that rather than treating quality assessment and control as unknowns of a cyber-physical production system, they are implemented as an integral part of it, aiming to create a scalable, and economically viable solution.
What are the expected outcomes and impacts of the openZDM project on the overall sustainability and competitiveness of European manufacturing industries?
openZDM aims to provide a set of enabling software and hardware solutions, integrated through a software platform, with a set of reference technologies for the implementation of each component, that will allow manufacturers to tailor it to their needs and environments.
In turn, the project’s enabling solutions will allow them to inspect in a cost-effective approach their production lines for defects and their root causes will facilitating online reconfiguration, proactively and in a non-destructive approach, increasing their sustainability and thus competitiveness.
How does the openZDM project contribute to the future of manufacturing?
The project aims at enhancing the digital capacity and capabilities of factories of the future by adopting some key digital technologies related to the management of production assets/processes, introducing advanced NDI tools, digital twins, and data analytics for online quality assessment.
This will lead to considerable improvements to factory flexibility, especially for re-configuring production capacity and processes, facilitating significant waste reduction, in the production processes as well as at an ecosystem level.
As such, openZDM is expected to support through its enabling solutions:
- Reduced raw material waste.
- Increased resiliency of production systems.
- Contribution to standardization for integration, communication, and control of manufacturing systems.
Short Biography
Dr Nikos Nikolakis holds a diploma (MSc. equivalent) from the Department of Electrical Engineering and Computer Technology of the University of Patras, a PhD from the Department of Mechanical and Aeronautical Engineering of the University of Patras, and a Master in Business Administration (MBA) from the open Greek university.
He works as a researcher in the Laboratory of Production and Automation Systems (LMS) and has participated in various European and nationally funded projects. In the context of the projects, he participated in the management, design and development of software components related to statistical and artificial intelligence, human motion recognition, regression analysis and modelling of cyber-physical systems mainly in the manufacturing sector.